

Vacuum Box - Vacuum box testing is used mostly for tank floors by creating a vacuum in a portable box with a soapy substance applied to the material and welding.Brinell Hardness Testing (BHT) - BHT is a quantitative method of testing the hardness of a material or weld by physically indenting the material and comparing the size of the indention to that of a twin indention of a known material hardness.VT requires that the inspector look at the surface of the part being inspected for a visual observation of the surface to evaluate the presence of surface discontinuities or conditions that do not follow procedures, codes or specifications. Visual Testing (VT) - VT is the most commonly used test method in the industry.Any internal reflectors, such as lamination or pitting, can also reflect the sound wave back to the sending unit. For thickness UT, the air at the backwall, or inside, of test part is the reflector. Ultrasonic Testing (UT) - UT testing is when ultra-high frequency sound is introduced into the part being inspected and if the sound hits a material with a different acoustic impedance, some of the sound will reflect back to the sending unit and can be presented on a visual display.Each chemical element emits X-rays at a unique energy. The atoms of the part absorb energy from the X-rays, becoming temporarily excited and then emit secondary X-rays. Positive Material Identification (PMI) - PMI is the analysis of a metal or alloy with the use of a handheld X-Ray fluorescent (XRF) instrument to establish the composition by reading the quantities by percentage of its constituent elements by exposing the Atoms to a beam of X-rays.Magnetic-Particle Testing (MT) - Magnetic particle testing uses one or more magnetic fields to locate surface and near-surface discontinuities in ferromagnetic materials.

#Cfs company code#
Once the excess penetrant is removed, the penetrant trapped in those voids will flow back out, creating an indication that can be evaluated and judged against a code or specification for compliance or as to the effect it will have on the services life of the part.

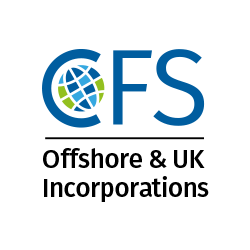
This map can be electronically generated in a 2D or 3D format with sizes and depths of pits easily determined for evaluation of remaining wall and remaining service life of the part. AUT Corrosion Mapping - AUT utilizes the phased array technology to create a map of the internal surface of the part being inspected.Multiple beams can be generated for a single examination, therefore, a variety of beams can examine the area of interest thoroughly. By phasing the pulses across the array of elements, the ultrasonic beam can be steered and focused as needed for a particular application such as weld quality evaluation, volumetric inspection of forging or cast materials, and mapping of erosion or corrosion damage in existing piping or pressure vessels. Phased Array Ultrasonic Testing - PAUT employs a probe composed of several small ultrasonic elements which are individually phased by the instrument.
